
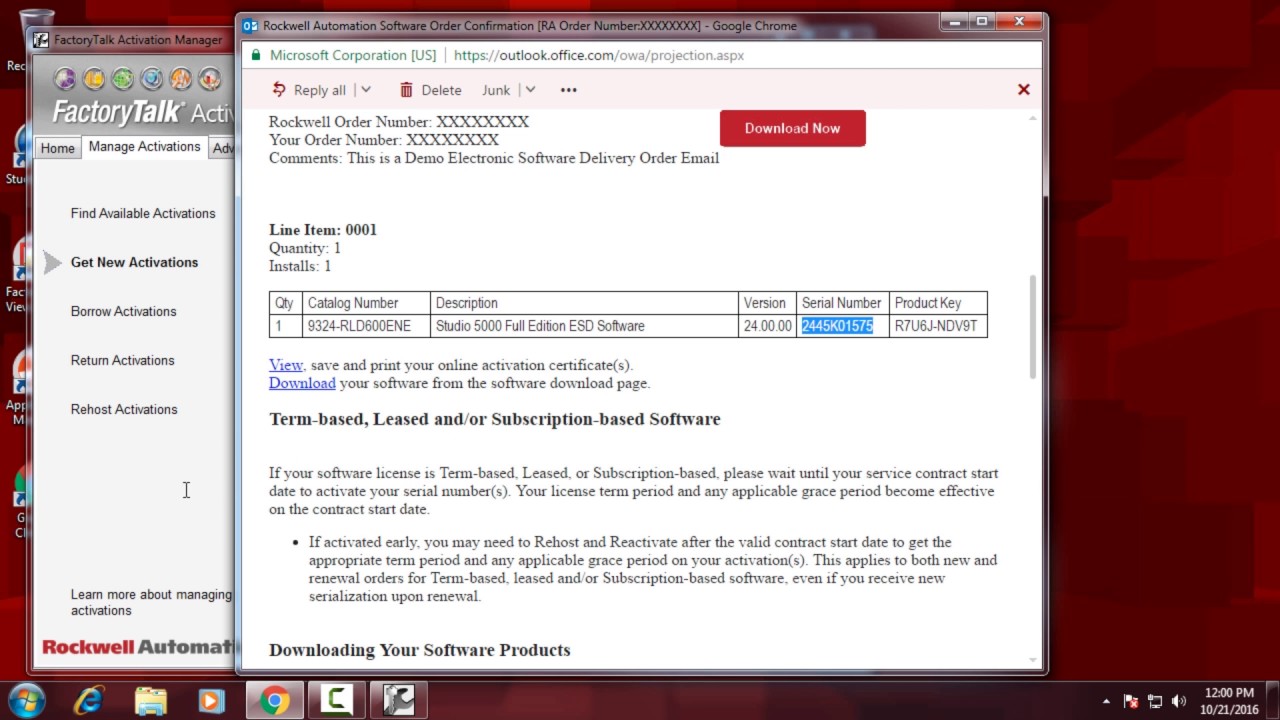
That is - the speed of selling cycles in the market has suddenly picked up, but order approvals are so administratively complex and slow that sellers are able to find more efficient channels. This example highlights how the administrative process of order approvals can, under certain market conditions, create a fundamental misalignment between selling tempos and procurement tempos, a misalignment that makes the market inaccessible. Thirty-six hours later, those approvals were secured but the PPE was no longer available.” When we presented our results, the client said that the cost was three times the approved threshold for PPE. Elouise Epstein’s book, “Trade wars, pandemics and chaos: How digital procurement enables business success in a disordered world," relating to sourcing PPE during March 2020: “Employing our best sourcing capabilities we managed to secure a decent-sized supply. But the underlying reason why certain companies have no problem sourcing lumber and others find it nearly impossible comes down to a little-known administrative process: order approvals.ĭuring a perceived shortage, the speed of the market picks up – people buy faster and faster, driven by the fear that they will miss out on a closing window of opportunity to secure available product.
#Rockwell factorytalk view studio download drivers
And in certain parts of the country it is challenging to find trucks and truck drivers – a distribution bottleneck. It’s not as if we have run out of trees or saw mills.

The lumber shortage is a perfect example of this. Critically, when there are constraints on the underlying distribution capacity – the network that moves product from one place to another – that’s not a shortage. One clear sign of a shortage is that it is impossible to get a material due to constraints on the underlying production capacity. A shortage occurs when demand exceeds available supply. To understand why, it is helpful to first define what a shortage is. The phenomenon we are experiencing is not a shortage – of either materials or labor.

But more often than not, the source of disruptions isn’t transportation and logistics, nor is it “just in time.” The real source of disruptions is constrained procurement. Or, there are people who blame the “just in time” manufacturing model, believing it’s time manufacturers went back to keeping more inventory on hand as buffer stock in case of future shortages. Have you heard people say: “There just aren’t enough trucks on the road?” Whenever there is a major supply chain disruption leading to a shortage, we tend to blame transportation and logistics choke-points. The reality is that port congestion is one tiny piece of the overall puzzle. One easy culprit might be port congestion – the lines of ships stretching so long out from ports like Los Angeles and Savannah that they are visible from space. It seems every industry and buying segment is experiencing its own sort of supply chain disruption. Even ketchup in restaurant to-go bags isn’t immune. Lumber and steel for construction companies.
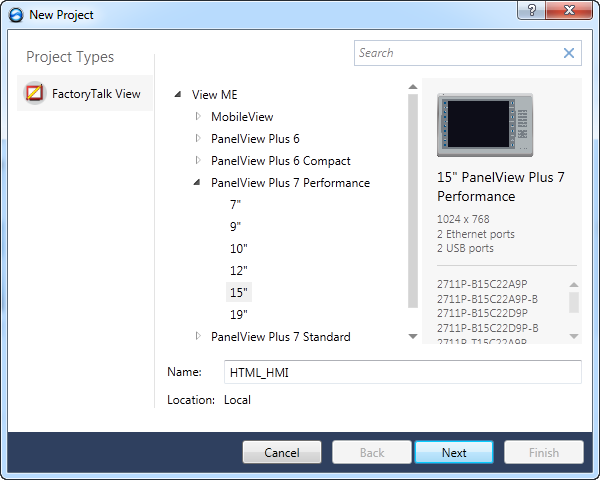
The question is: are empty shelves here to stay? We are still seeing them at major retailers for everything from electronics to hamburgers.
